Joseph Clayton - tanners of distinction
Finding the right leather for Calder cases was not easy. I wanted leather that was supple enough to hug the carbon fibre shell, would take years of use and still look handsome.
Months of research finally led to my being introduced to Joseph Clayton of Chesterfield. Clayton are one of the last tanners in Europe still using the painstaking pit-tanning method.
A small company with a worldwide reputation Clayton's clients range from blue chip Italian and American designers to the heavy industry.
Claytons specialise in making leather to their clients' exact specification - and that is what they have done for us.
Hides for Calder go through a vegetable die process taking 3 months from start to the rough-tanned 'crust' stage. After careful selection of hides of the right quality the bespoke dyeing & finishing takes a further 4-5weeks.
To achieve the exact look we wanted our leather is finished by 'tipping' a hand application of a contrasting dye that makes the peaks of the embossed print stand out.
John Avery and Barry Knight at Claytons are both deeply knowledgeable and passionate about creating great leather. They took me round the works - a truly extraordinary place steeped in history.
Hides coming out of the first stage of the process
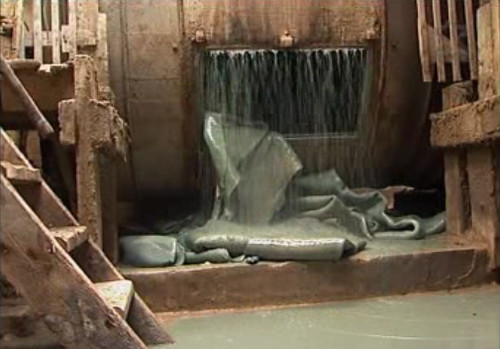
Moving a hide through the pits
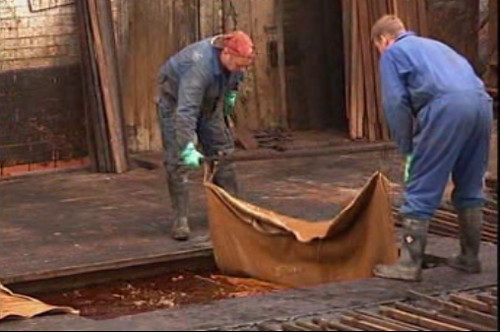
Checking the thickness of leather
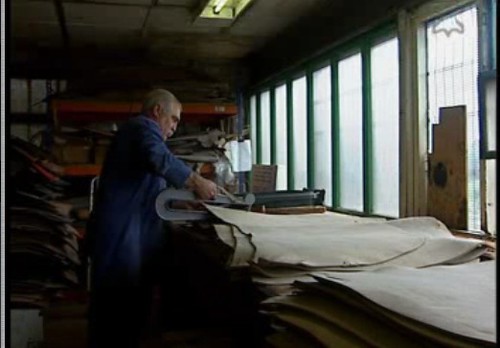
category:
Calder blog home page
Calder website home page
Months of research finally led to my being introduced to Joseph Clayton of Chesterfield. Clayton are one of the last tanners in Europe still using the painstaking pit-tanning method.
A small company with a worldwide reputation Clayton's clients range from blue chip Italian and American designers to the heavy industry.
Claytons specialise in making leather to their clients' exact specification - and that is what they have done for us.
Hides for Calder go through a vegetable die process taking 3 months from start to the rough-tanned 'crust' stage. After careful selection of hides of the right quality the bespoke dyeing & finishing takes a further 4-5weeks.
To achieve the exact look we wanted our leather is finished by 'tipping' a hand application of a contrasting dye that makes the peaks of the embossed print stand out.
John Avery and Barry Knight at Claytons are both deeply knowledgeable and passionate about creating great leather. They took me round the works - a truly extraordinary place steeped in history.
Hides coming out of the first stage of the process
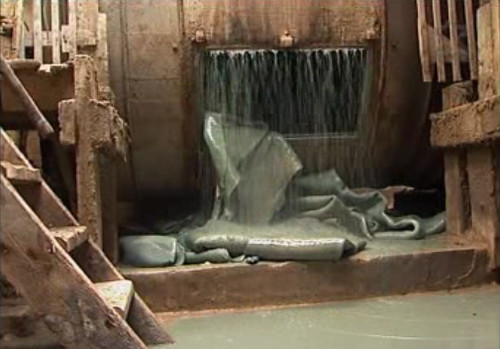
Moving a hide through the pits
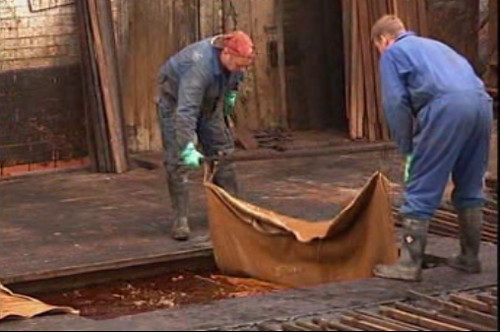
Checking the thickness of leather
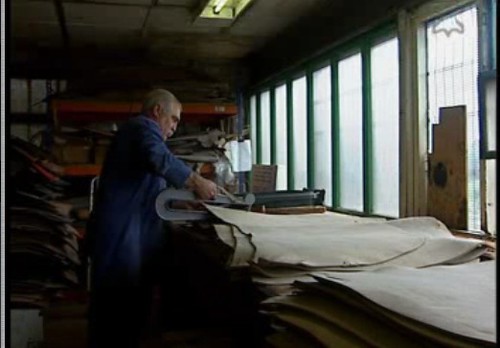
category:
Calder blog home page
Calder website home page
0 Comments:
Post a Comment
Subscribe to Post Comments [Atom]
<< Home