Handle re-design CAD image
Barry Noble has worked up some CAD images of what the new handle design will look like. Always looking to keep the design as simple as possible we've decided to shorter the handles and have the attaching screws covered by leather recessed into the stainless steel handle plate.
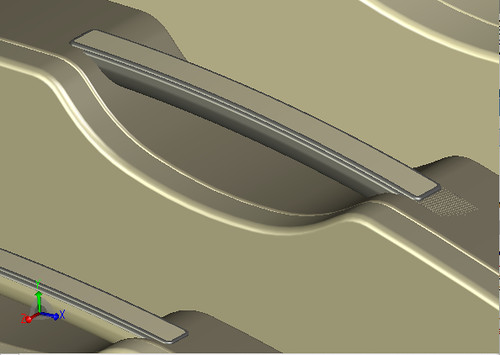
category:
Calder blog home page
Calder website home page
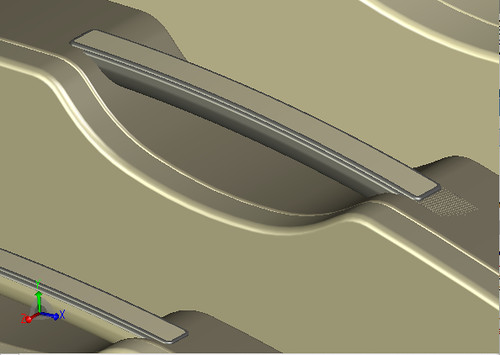
category:
Calder blog home page
Calder website home page
4 Comments:
I dunno, I really liked the aesthetic of the previous, stainless-only handle design. I think this breaks up the otherwise very clean visual lines. The only thing I would suggest in lieu of this modification is to cover the bottom of the handle and leave the top unscathed for 2 reasons.
1. Metal handles get cold and stay cold, and for stringed-instrument musicians a cold hand is not a happy one. (This is especially true for odd guys like me and many women who have Reynaud's syndrome, which limits circulation in the hands and feet, better known as why-your-wife-has-freezing-feet-in-bed-syndrome.) If you cover the bottom of the handle with insulating material like leather or wood then the gripping portion of the hands won't freeze up as easily.
2. Inlaying that leather into a tiny pocket will not be an easy operation. Milling the pocket into the handle with sharp, 90 edges to match the leather cut edge will require a square endmill and at least a 4-axis CNC machine. If you use a 3-axis with a ball endmill you'll have poor up-close finish quality. Moreover getting it to fit just so will not be easy and it is here where the dangers of CAD designs rear their heads: looks great rendered, but impossible to replicate. Putting the inlay or wrap underneath the handle makes your life easier because it's far harder to scrutinize.
In any configuration, gluing in leather to metal so it lasts a long time in a high-wear configuration will not be easy. It's going to want to peel out of its pocket after being held and hand-abraded over and over again and when its corners start to peel it won't make your customers who bought $5000 boutique cases very happy.
I'd recommend a full-leather solution or a full-stainless steel solution. For my money, (which you probably won't get because I'm poor) I think the SS mockups were super sexy and the leather ones rather bland an indistinctive.
-Dave
P.S. I'm going to email you soon personally, I have a question for you to take out of the public arena.
Dave - I'm very grateful for your thoughtful comments.
I've been concerned about the cold hand sydrome for some time - guitarists from Canada told me this was a big issue for them.
Barry and Johan - engineer and leathersmith believe the technical side is not a problem - and I will go with their advice.
The leather will be inlaid slightly below the level of the steel and with modern glues peeling should not occur. High end cameras (Leica etc) have used this technique for over 50 years without problems.
I too liked the raw SS look - and it was only after I'd carried a prototype case around for a day that I realised that the steel was hard on the hands and also stood out too much from the leather.
For me the leather inlaid with an edge of steel showing is a more satisfactory way to combine the two materials.
Nick,
I looked over some of the old images again and noticed a few things I'd overlooked and think you're fine. I realized that your old handle was composed of a leather lower with a sheet SS handle which was probably manufactured by:
1. CNC milling the shape (corner with filleted corners)
2. CNC milling the edge fillet
3. CNC countersinking the screw holes
3.5 CNC engraving teh logo if you have one in hte final version
4. Flipping the workpiece and CNC milling the backside edge fillet
5. Bending milled handle over curved form
If this is even close then milling another pocket into flat stock will be very simple, though I wonder if have a subflush leather cover is all that useful (but that's why you and yours are prototyping, not me).
The issue with not-peeling and modern adhesives is more a matter of coverage. If you don't want the edges to curl you must adhere them, which can result in glue squeezeout if you're not very careful. Additionally I would expect line-to-line matchup to be very tough even in a hand-produced setup.
In any case, more power to you as your design is refined. One last note on aesthetics: I began to think, subtlely over time, to think of your stainless handle over your matte black shape as an important part of the case's visual signature. I hope that with the smaller SS outlines your case retains some of its distinct and unique appearance, though I fear by making the handle blend into the case you lose a bit of identity and branding. Food for thought.
-Dave
Dave you are right about the process by which we make the steel element of the handle. I also agree that we will need to be skillful with gluing the inlaid leather.
In my earlier reply I forgot to mention that I have spent weeks on refining the handle. I was convinced that the plain steel sheet was too obtrusive. I explored having the steel photo-etched, lazer etched and rejected both.
Machine turning seemed the best option and I was on the brink of prototyping some handles with a simple machine turned pattern when I came up with the idea of inlaying the leather.
Until we have made up some sample handles and I have lived with them for a while I will not be sure that it is the right answer. (I've lived with the present steel handle design for over 6 months and only very recently realised it was not quite right.)
For me the leather inlay works because it makes the look of the case simpler and I have a passion for simplicity. Up til now I've really liked the look of the allen key type screw heads - and so it is a big step to hide them.
Once again thanks for your interest.
Nick
Post a Comment
Subscribe to Post Comments [Atom]
<< Home